Introduction
SMA Mineral supplies products based on the carbonate minerals limestone and dolomite. Raw materials obtained directly from nature are refined into complex end products that are used and are absolutely vital in a number of different areas.
But how are our products actually produced? How do they differ and what processes do we have to carry out?

Most of our products start with lime and dolomite.
These minerals are naturally occurring in many parts of the world but vary enormously in terms of their quantities. In Sweden, lime and dolomite are primarily found in southern and central Sweden, but areas in our neighbouring countries also have rich deposits of the minerals.
SMA Mineral has its own lime and dolomite quarries in Sweden at the Jutjärn, Berga, Stucks and Gåsgruvan mines. We also have our own deposits in Norway and Finland, and also in Estonia and Bulgaria.
In a limestone quarry, the raw material is often blasted or drilled from the rock. It may also be possible to simply excavate the limestone because it is so young. The newly quarried limestone is made up of large particles of relatively coarse fractions.
Limestone can only be quarried with environmental and water permits obtained from the Swedish Land and Environment Court. Aspects such as water treatment, impact on the natural environment, and how noise and dust will be handled are subject to thorough scrutiny before permits are issued.

Once the limestone has been mined, it is taken to a crushing station for fractionation. The crushing station is usually located next door to the limestone quarry, but sometimes the stone is transported to the lime works for crushing/grinding.
The limestone is processed into a wide variety of fractions and sizes. Crushed stone for road, construction and infrastructure projects can measure between 20 mm and 70 mm in diameter.
Other limestone is ground and screened to produce limestone flour used in the manufacture of products such as animal feed or for liming in agriculture and forestry. SMA Mineral supplies a range of finished products for all sorts of applications.
The most finely ground fractions can be used as additives in paint and plastic products, for example.

For many applications, burning is required to give the products the necessary properties.
Burnt lime and burnt dolomite are produced in a process in which roughly crushed stone, is heated in a shaft furnace or a rotary kiln to temperatures of around 1,100 °C. In this process – often called calcination – the limestone is broken down into calcium oxide, known as burnt lime. Dolomite is also put through a similar process.
After burning, the burnt minerals are crushed into fractions suitable for their intended application. Burnt lime is used in areas such as the manufacture of iron and steel, cellulose production and the mining industry. Burnt products are also used to treat water and flue gases. Finer fractions of burnt lime are also used in the production of slaked lime.
SMA Mineral burns lime and/or dolomite in about ten of its plants around Europe.
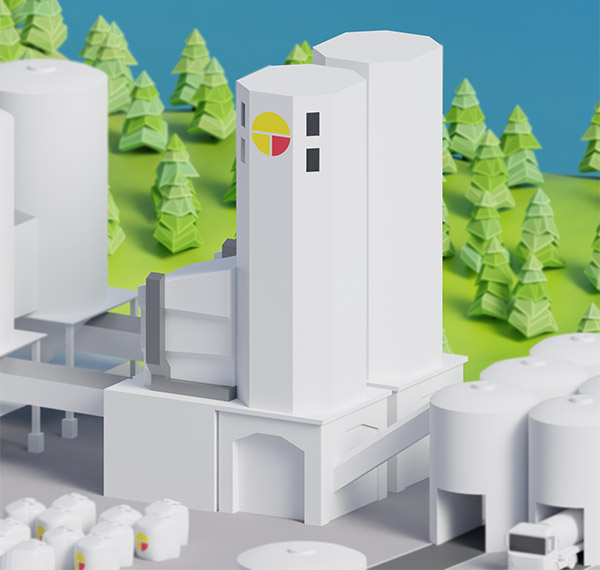
Calcium hydroxide – so-called slaked lime – is formed when burnt lime is allowed to react with water under controlled conditions. During the slaking process, a dry, fine-grained powder or paste with antibacterial, disinfecting and acidifying properties is formed.
Slaked lime has many applications. It is used by construction chemical manufacturers as an ingredient in bricklaying and paving mortar, for example. Slaked lime is also used in agriculture and for treating flue gases and water.
SMA Mineral produces slaked lime at its plants in Rättvik and Röyttä in Sweden, as well as in Dobromir and Troitza in Bulgaria.
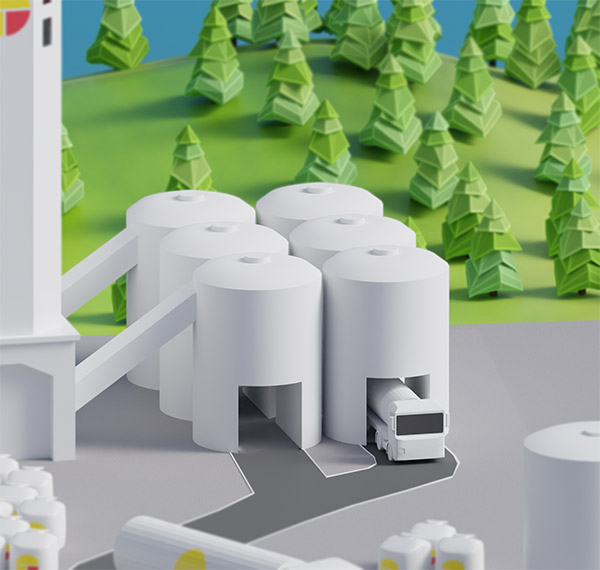
Different types of lime are sometimes mixed with each other or with other substances in order to optimise the properties of the end product.
A good example of this is SMA KC Binder which uses burnt lime mixed with cement. Other common mixtures are Spectra and Cement. Burnt lime can also be mixed into limestone to produce structure lime for use in agriculture.
Mixing can be carried out at the lime mill, at one of our terminals or at the customer’s premises.
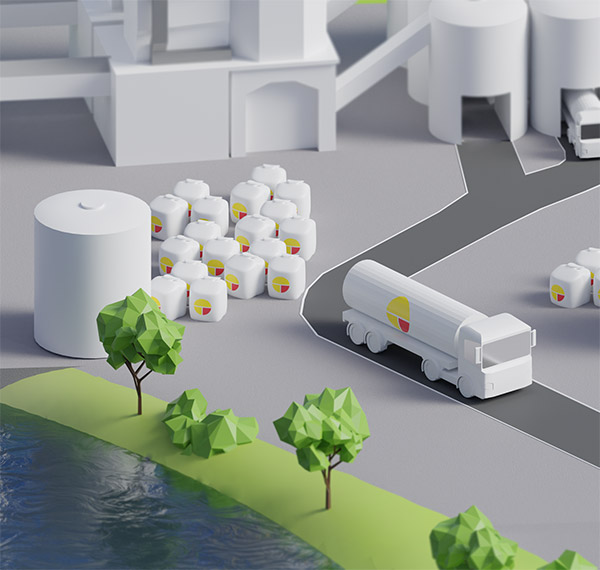
Our products are delivered in bulk, or packed in large sacks or smaller quantities.
The lime is often delivered directly from our limestone quarry to the end customer, but we also deliver large volumes via terminals in Otterbäcken, Kolbäck, Söråker and Åbo/Rauma.
The terminals are strategically located around Scandinavia in order to be close to our customers, primarily in the paper and cellulose industry. This proximity improves availability and has a positive impact on logistics and the environment. The terminals are owned and operated by external operators. SMA Mineral rents silo spaces in the terminal for storing mineral products.
Most of our lime is transported by road. Trains are used in exceptional circumstances, such as when transporting lake lime to Norrland. Ships are used primarily to collect raw materials from external lime quarries and for deliveries to/from our terminals.
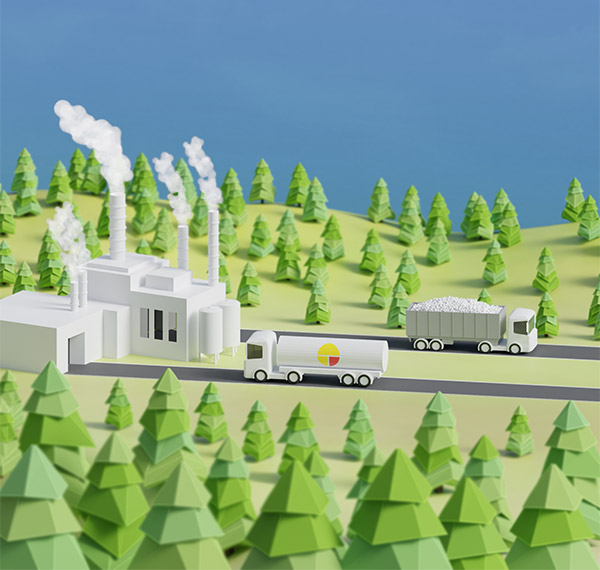
The sulphate processes in the paper industry require large quantities of lime. Lime in its burnt form is needed to recycle the chemicals in the process in a sustainable and environmentally safe manner.
Many paper mills choose to work with newly produced burnt lime. An alternative method, with the same end result, is to use lime sludge, a residual product from sulphate production that occurs during the preparation of so-called white liquor. The lime sludge is burned at the mill, or in collaboration with lime producers such as SMA Mineral, to create lime.
Our partnership with SMA Mineral means that lime sludge from the sulphate process is collected from customer premises and brought to SMA Mineral’s lime mill in Sandarne where it is burned in a lime kiln to produce lime.
The lime sludge is sometimes mixed with newly produced lime in order to further enhance the properties of the material. The final product is transported and reused in a circular process as part of the mill’s pulp production.